Process Chiller
What is a chiller?
A Chiller, also known as a water-cooling chiller, is a special category of cooling systems that is specifically engineered to cool fluids down, more commonly water. While their heat pump serves to heat fluids, the evaporator is smaller than its counterpart from air coolers and the water circulation system operates by mechanically pumping an external input flow.
As this type of equipment uses water, gas or evaporative fluid as a medium to cool down, they are considered the best option to climatize big facilities, office buildings and, especially, all places where both climatization and domestic hot water (DHW) systems are required, such as hotels and hospitals; however, they can also be applied to industries in absolute need of heat dissipation processes for equipment and reactors.
TYPES OF AVAILABLE/EXISTING CHILLERS
A chiller consists of the following main components: a compressor, a water-cooled or air-cooled condenser, an expander element and a control panel.
- Water-cooled chiller
This equipment consists of a variety of external continuous sources of water, such as cooling towers and fluid coolers; the chiller is mounted inside to help increase the operating useful life of these compact units, which work silently and despite being featured with high energy efficiency, they need
more maintenance and cost more than the air-cooled alternatives.
- Air-cooled chillers
This equipment uses ambient air to remove heat from industrial processes and is ideal for limited indoor spaces, as they are placed outside.
HOW DOES A CHILLER WORK?
The chiller evaporator, compressor, condenser and expansion device are each subjected to a thermodynamic process during the cooling process; the chiller operates in the following four stages:
1. First, the chiller evaporator acts as a heat exchanger, where all heat collects and carries process water heat to the cool liquid refrigerant inside the chiller, then, the heat process increases the refrigerant temperature, causing a shift from a low-pressure fluid to a low-pressure gas, while the process refrigerant temperature also decreases. ** The condenser can be a plate or shell and tube heat exchanger.
2. After that, the low-pressure gas enters the compressor, where it will increase the upcoming refrigerant gas pressure until it reaches a sufficient high temperature to dissipate heat from the condenser.
3. In the condenser, the refrigerant gas shifts back to liquid; ambient air or condenser water removes the heat from the vapor-to-liquid conversion process, depending on whether you have an air-cooled chiller or a water-cooled chiller. ** The condenser can be a plate or shell and tube heat exchanger.
4.-The last stage of the cooling process consists in the liquid refrigerant traveling to the expansion valve, where it is quantified before it enters the evaporator where the cooling process is replicated once again.
Basic information for a proper selection
- Application
- Type of working chiller (water, air)
- Input and output temperature of the water process
- Flow or volume of flow
- Type of working refrigerant
- Available voltage
APPLICATIONS
- Food industry
- Big facilities climatization
- Process engineering
- Cooling products
- Cooling equipment
- Injection molding
- Tool cutting
- Chemical products
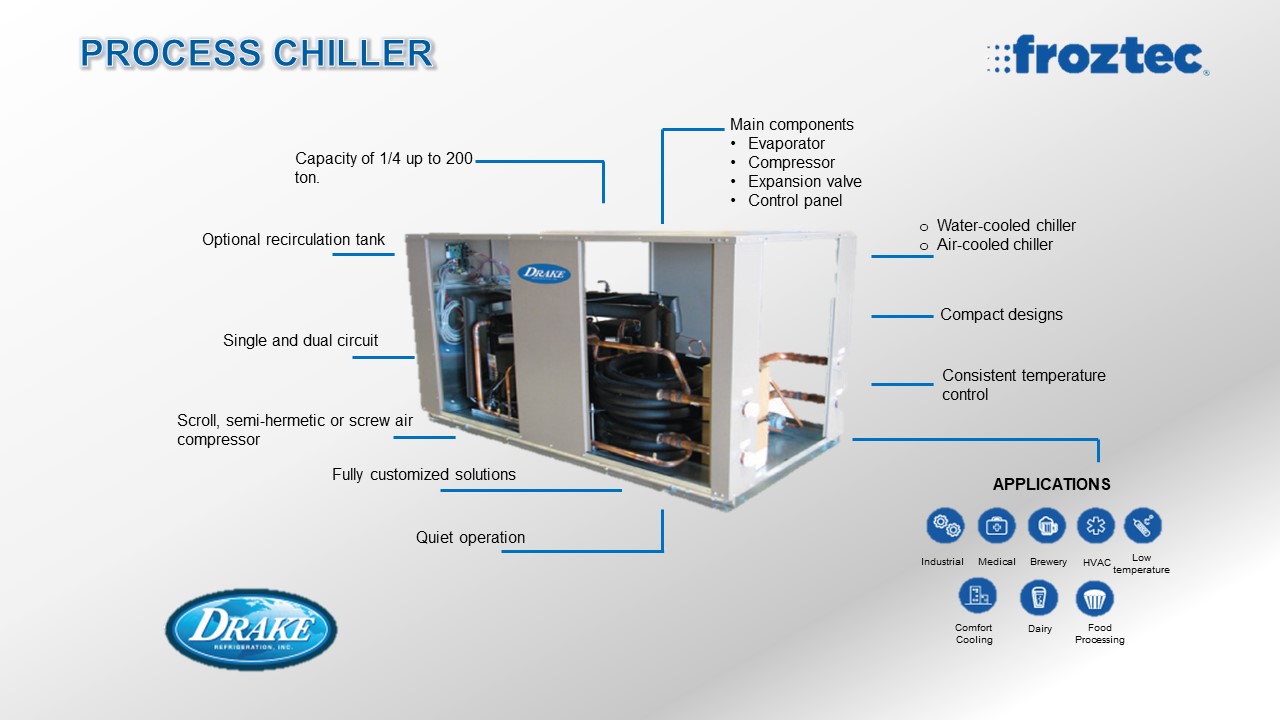
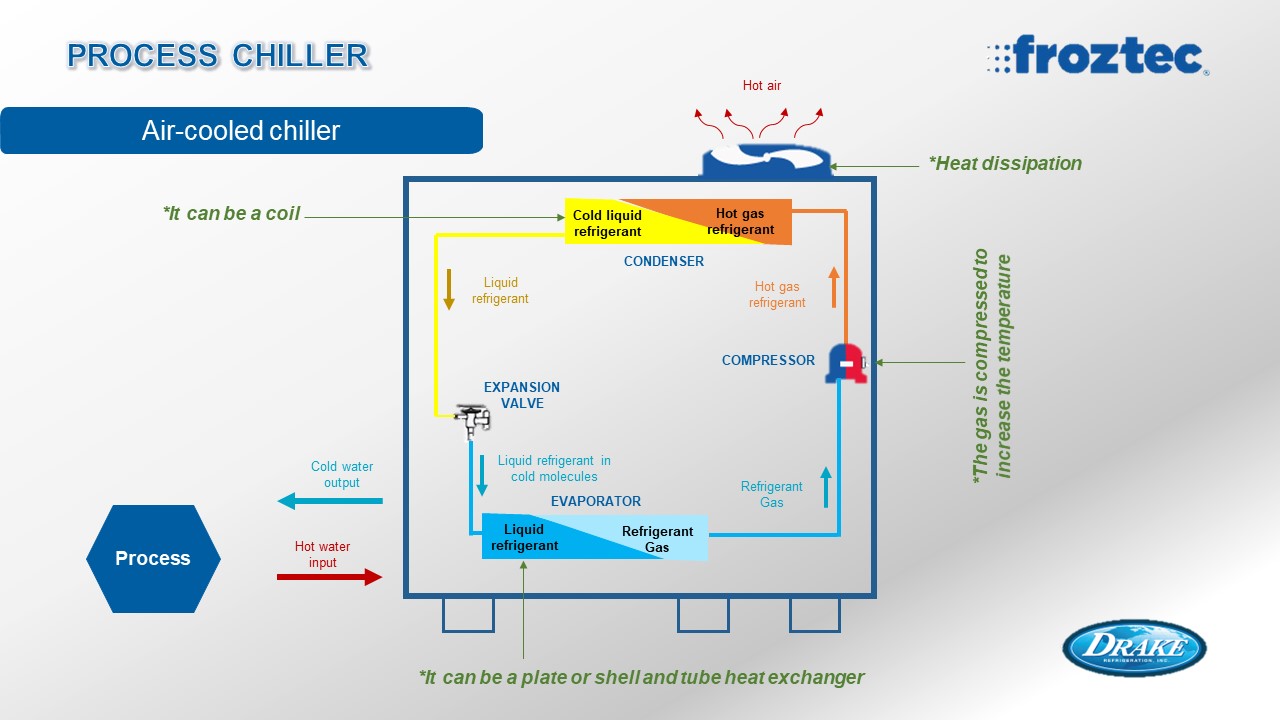

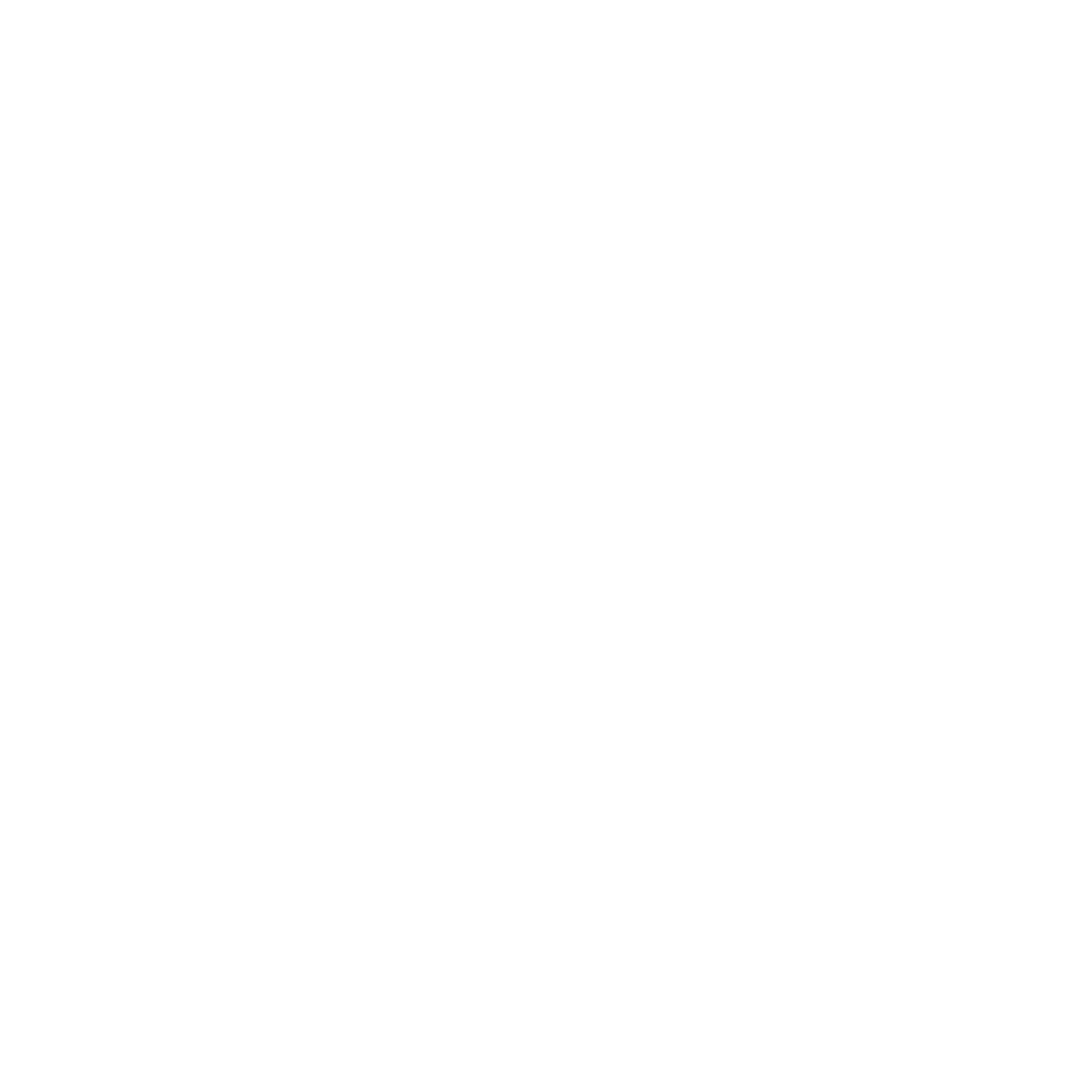